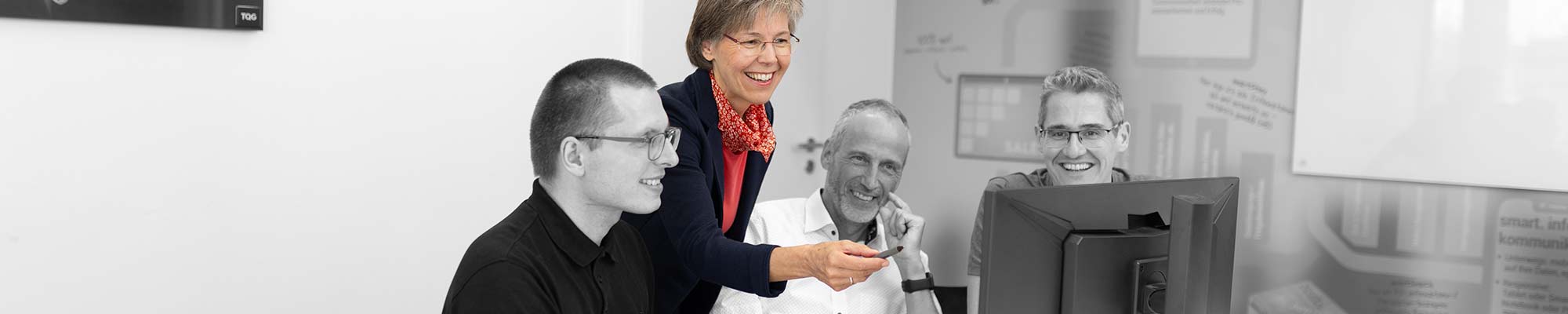
The digital twin in Industry 4.0
Two is Better
Steffen Krause, Executive IT Architect, Cloud Application Development, Internet of Things at IBM Global Business Services Europe
Published in: DiALOG - THE MAGAZINE FOR ENTERPRISE INFORMATION MANAGEMENT | MARCH 2019
The digital twin in Industry 4.0 is currently one of the hottest topics in the industry and is still uncharted territory in many cases for the companies that use it. It is a digital representation of a product that mirrors its real-life counterpart. In short: the digital twin is the link between the digital and real worlds.
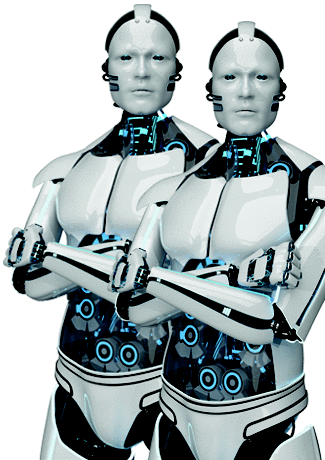
In its complete definition, the digital twin covers the entire life cycle of a product or object. This means that it starts with the definition of requirements, continues through simulation and production to utilisation, and ends with dismantling or disposal. The more parameters describe the digital twin and the more timely and comprehensive the relevant data is, the clearer its image of the real object becomes. Data is the central keyword: it is the twin's lifeblood, without it it would not exist. The digital twin in Industry 4.0 is fed with data that is collected by sensors, for example, and transfers the specific production parameters or its current utilisation into the virtual world. Ideally, this takes place over its entire lifetime and the twin often has several types of data - from design, production and utilisation. This means that the twin always "knows" what its physical counterpart should be and is like at all stages of the life cycle.
For example, companies can test the product throughout the entire development process and later compare the simulated tests with real usage scenarios. In this way, product development adapts to real requirements and no longer to abstract scenarios. This means that products are improved where it makes sense.
The digital twin doesn't stop at the factory
The journey of the digital twin does not end with the delivery of the product. Only now does one of the most insightful phases begin for every product developer, provided they have access to the relevant data: How does the product perform in real-life operation? Sensor data provides information about usage behaviour, necessary maintenance or user preferences, but also reveals any backlog or modification requirements. This data from ongoing operation is important for verifying assumptions made for the product design or, if possible, correcting them during the product's lifetime. Software-based properties in particular can often be adjusted during the product's lifetime. The data therefore provides important impetus for improvements in future product generations. The journey of the digital twin in Industry 4.0 as a virtual companion alongside the physical product only ends with disposal, where it can provide valuable information on the recycling of components, for example.
Here to stay
The digital twin approach is not new, but there are significant technological changes that are currently driving the penetration of the concept forward. On the one hand, data can be collected worldwide more cost-effectively than ever before using sensors and gathered on cloud-based IoT platforms. This enables even less valuable products to be instrumented with inexpensive data. Generating useful knowledge from the collected data is becoming a key differentiator. Driven by the drastic fall in the cost of analytical algorithms and artificial intelligence, these capabilities can now also be economically viable for small use cases thanks to usage-based cloud resources. The fact that data can be used to improve products or even establish additional business models supports the success of the digital twin in Industry 4.0 all the more. This includes, for example, analyses relating to faults or downtimes, the condition of machines and components - findings with a direct influence on key differentiating features in the market.
The application areas are the starting point
However, we must not forget the current hype: The decisive factor is the use cases that require a consistent digital image and therefore drive the concept of the digital twin. In principle, there can be many reasons for this - from improving service and reducing development costs to new data-based business models. It makes little sense to simply collect a lot of available data and believe that added value will be found. What is likely is that without a clear objective, the digital twin in Industry 4.0 will become a worthless data tomb. From a technical perspective, it is often underestimated that it is not about collecting easy-to-obtain data, but about collecting the right, necessary data and the dependencies and connections that exist between the data. In some cases, access to this data is very time-consuming and there is insufficient understanding of the interrelationships. Furthermore, it is often underestimated in the production and operation of the product that the information in the digital twin should be collected synchronously and as close in time as possible, as otherwise cause-and-effect chains are difficult to determine.
Analyses prove impact potential
When introducing a digital twin, it is advisable for companies to develop one or a few use cases that ideally deliver high added value for the organisation or customers. Based on these objectives, a gap analysis can be carried out to identify the areas that require improvement. During these phases, it is often found that access to important data-holding systems is very difficult or that there is too great a variety of interfaces that can hardly be handled with realistic effort. This gives rise to initiatives that tackle such challenges, for example through the use of integration tools or the exchange of instrumentation or the use of open standards.The fundamental change is that the existing competencies are no longer viewed from a vertical perspective, but from an overarching horizontal perspective that enables new optimisation potential. This means that the upheaval caused by the digital twin is not a purely technological consideration, but can also have significant organisational effects.
Innovation forms the core of IBM's strategy. In order to support companies of all sizes in the digital transformation of their business models and to harness the opportunities of digitalisation for them, IBM is focusing on the growth initiatives of artificial intelligence (AI), business analytics, cloud computing, blockchain and security. For IBM, these strategic fields form both the basis of its constantly expanding solution portfolio and the foundation of its ongoing transformation into an AI and cloud platform provider.
www.ibm.com
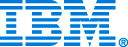