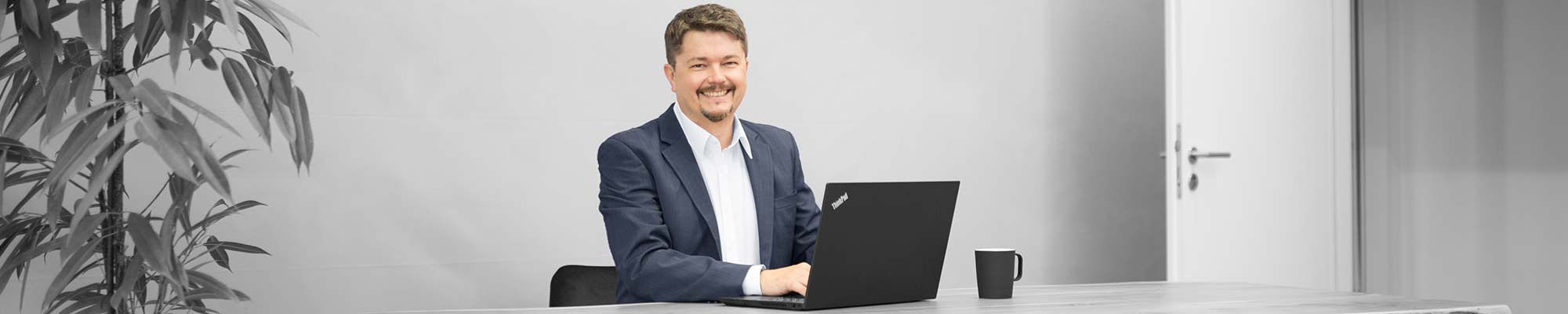
Information by Compliance
DiALOG Award winner 2015: Electronic workflows accelerate the sales process at TIGGESRalf Klemm, Head of IT at TIGGES GmbH and Co. KGy
Published in: DiALOG - THE MAGAZINE FOR ENTERPRISE INFORMATION MANAGEMENT | MARCH 2016
TIGGES combines the traditional promise of quality ‘Made in Germany’ with efficiency and cost-effectiveness to create its own entrepreneurial character trait. Complemented by service expertise, professional qualifications and personal commitment, this results in a corporate culture of absolute reliability, in which corporate compliance is very important. It is practised by all management levels and defines a unique selling point, the success of which is an obligation.
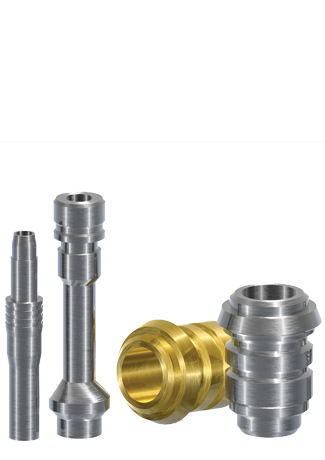
Technologically, TIGGES has always been at the cutting edge, as the company constantly and consistently invests in all production technologies. However, the increasingly important topic of Enterprise Information Management (EIM) had been somewhat neglected at TIGGES. In 2008, the quotation and order folders alone still contained around 1500 active processes. The information was only stored in one place, and accessing it was time-consuming and costly. Some things were left lying around or disappeared, there was no scheduling and it was difficult to maintain an overview. TIGGES therefore planned to introduce an EIM system. They chose ELOprofessional, from ELO Digital Office GmbH, Stuttgart, not only because of its user-friendliness and integration capability, but also because it allowed them to realise the planned ‘folder cycle’ workflow - from enquiry to calculation to invoicing. All departments and decision-makers were involved, i.e. the entire company. With ELOprofessional, parallel processing is now possible, there are waiting points, an information transfer for subsequent departments - and all information and documents are visible to users at all times (depending on the ELO authorisation level).
Archive connection to TIGGES ERP
The archive structure for the project storage was designed according to clear specifications: The employees can find themselves in the colours and structure, but as few entries as possible should be made by the users in order to avoid any kind of ‘self-realisation’. This means that ELO specifies almost everything (filing path, indexing, etc.) and a workflow even controls the deadlines for order monitoring. Employees can search for projects or enquiries using keywords, among other things - via an interface also in the existing ERP system. ELO COLD also enables the fully automatic archiving of mass data from central business applications (e.g. ERP system, MS Office applications). All processes are documented by ELO and remain traceable (optimum transparency).
Information by Compliance
In the beginning, there were around 50 active ELO users at TIGGES. Today there are almost 80 and all TIGGES Group locations (including Taiwan and the USA) are now integrated. The system runs optimally and impresses with its great benefits for the company, as the ELO workflows enable the Tigges Group to accelerate the sales process from the request for quotation to feasibility studies and order planning. Workflows between the non-European locations and the head office in Germany have been significantly optimised and data is exchanged in a controlled manner in accordance with company compliance.
ELO workflows control the processes
The following example shows a brief process flow: As soon as an enquiry is received (by fax, e-mail or post), it is entered into the ELO EIM system and the workflow starts, initially until the quotation is submitted. Until then, the feasibility is checked according to a defined set of rules (decision-making). The workflow guides all users through the set of rules, querying and collecting information and partial decisions. All documents for decision-making can be accessed directly via the EIM ELO. If feasibility is confirmed, the offer is submitted. If the customer then places the order (by fax, e-mail or post), it is entered into the ELO EIM system with reference to the enquiry process. The workflow now guides all users through the production process, again requesting or collecting information. Here too, all production and QM-relevant information can be called up directly via the ELO EIM.
All areas benefit from ELO
Sales, purchasing, controlling, design, costing, order planning and production (all departments and in all locations) benefit in particular from the use of the ELO EIM system. ELO users are now able to provide information on the current status of a sales, procurement or production process at any time. In addition, information is available to employees in real time. Searching for information across different locations is therefore very quick and easy. The cross-location workflows also make it possible to control the non-European locations from the headquarters in Wuppertal.
Sustainability through documentation
The particular sustainability of this ELO project lies in the automated documentation of all company processes, which runs automatically ‘on the side’, so to speak. This means that questions relating to the order placement can be clarified with customers and employees even after a product has been delivered. As the work steps are specified automatically, nothing can be forgotten. This sustainably increases the quality of the products and order processing, reduces the complaint rate and thus increases customer satisfaction even more. There are plans to utilise the ELO EIM system even more extensively in the future. This includes document-replacing scanning and, above all, the use of mobile applications. The ELO for Mobile Devices app will ensure greater mobility in business and thus make business processes location-independent. TIGGES also intends to adopt the overall concept for other locations.
DiALOG Award: Winner 2015
Thanks to the use of the ELO EIM system, all work processes can now be tracked transparently at all times and no work step can be forgotten. There are no media disruptions, no unnecessary duplication of work and employee motivation has increased. Following an evaluation of the submitted entries by a panel of experts, TIGGES wins the DiALOGAward 2015 against renowned competitors and thus follows last year's winner Porsche. The DiALOGAward is a seal of quality that TIGGES Managing Director Jens Tigges is very pleased about: ‘This award shows the quality standards of our company, which include not only the products but also the processes, and that quality always prevails in the long term.’ TIGGES GmbH und Co KG , Wuppertal, with locations in Taiwan, the USA, Malaysia and Japan, has stood for quality and expertise for around 90 years. The family-owned company is a leading specialist manufacturer of fasteners and a competent and experienced supplier partner and solution provider for many sectors, industries and customers worldwide. In the company's own cold forming, machining, grinding and hot forming departments, highly technical, modern and precise processes are used to produce exactly what the customer requires: a reliable fastener that delivers what it promises.
www.tigges-group.com
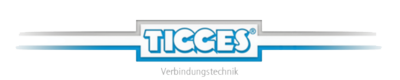